Společnost FMP má tři závody. Ten ve středočeské obci Ládví se zabývá především lisováním plastů se specializací na kombinované prvky mosaz – plast. Probíhá zde také montáž finálních výrobků a nástrojařská činnost. Technologie provozu je tvořena 14 vstřikovacími lisy, roboty na zakládání, sušicími jednotkami, nasavači, robotizací montáží sestav kulových ventilů a pomocnými periferními zařízeními. K dispozici je zde také kompletně vybavená nástrojárna s elektroerozivní hloubičkou, drátovkou, frézkou na výrobu elektrod a přesnou CNC frézou. Finální produkty, které ve zdejších světlých a dokonale čistých výrobních halách spatřují světlo světa, jsou ze 70 % uzavírací prvky pro vodoinstalatérské použití, konkrétně kulové a přímé ventily. Dále se zde lisují produkty pro oblast automotive, jako podvolantové jednotky, části spínačů a podobně. Zpracovávají se zde jak plasty technické (PA 6, PA66, POM, ABS), tak průmyslové (PPR, PPR-CT). Provozovna je nástrojařsky soběstačná, provádí si opravy a údržbu výrobních nástrojů, především forem, ale i vyrábí nové formy. Většina produktů FMP končí v zahraničí prostřednictvím českých odběratelů. Mezi ně patří například společnost Wavin Ekoplastik, FV Plast či Hronovský.
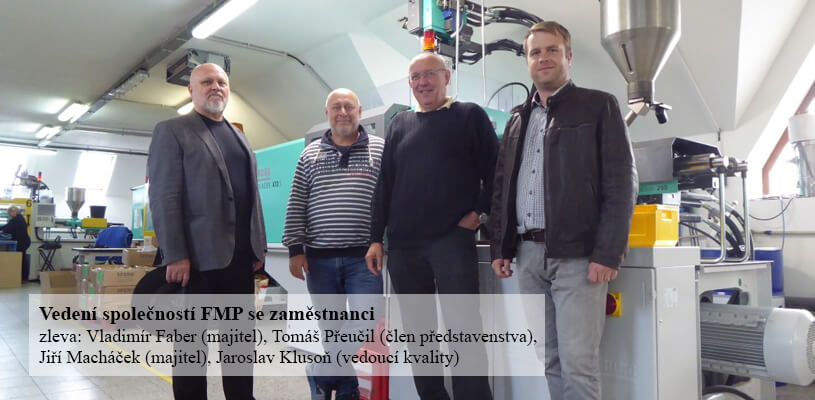
Kde na to vzít?
Firmu v roce 1991 založili společně tři kolegové strojaři, pánové Faber, Macháček a Pazderka – odtud název FMP. Po tragickém úmrtí pana Pazderky se v současnosti na vedení společnosti podílejí pánové Faber a Macháček a paní Pazderková.
„Když jsme se rozhodli založit vlastní firmu, měli jsme všichni tři asi 10letou praxi ve výzkumných ústavech technického zaměření,“ vzpomíná Vladimír Faber. „Začali jsme menšími zakázkami za pomoci subdodavatelů, ale brzy jsme zjistili, že tudy cesta nevede, že si musíme kompletní výrobu zajistit sami. Tak jsme zbourali moji garáž a na jejím místě jsme postavili první halu a koupili první dva stroje, automatické soustruhy na obrábění dílů pro potrubní systémy. V tomto oboru pokračujeme dodnes, avšak s velkým sortimentem a objemovým navýšením.“
Doba, kdy začínali podnikat, přinášela velké příležitosti, avšak problém představoval nedostatek vlastních prostředků na rozvoj. Když se pánové rozhlíželi po zdrojích, zjistili, že pokud si vezmou půjčku od některé z bank, které znali, budou muset počítat s úrokem ve výši 17–21 % ročně z vypůjčené částky a současně musí zaručit úvěr vlastním majetkem (a to v době, kdy například v Německu, v rámci podpory rozvoje podnikání, byly úroky 3,5 %).
V podstatě náhodou se však v té době – bezmála před 30 lety – dozvěděli o možnosti podpory ze strany Českomoravské záruční a rozvojové banky, která poskytovala jak ručení, tak i příspěvek na úrok.
„Velmi jsme oceňovali přístup ČMZRB, kdy s námi, jako novou firmou, začali spolupracovat,“ konstatuje Vladimír Faber. „Bez tříletých výkazů a zaručení násobkem poskytnutých prostředků, což komerční banky vyžadují. I při následné spolupráci s komerčními bankami, jsme hojně využívali produkty ČMZRB, ať už šlo o investiční projekty, podpory úroku nebo záruk za provozní úvěry. Během těch 30 let jsme v naší skupině za pomoci ČMZRB zrealizovali zhruba 15 projektů, z nichž každý byl ve své době významný a posunul nás kupředu. Důležité ale na tom všem je, že rozvojová banka vám nedává dotace, přispěje na úrok, nebo jej za vás dokonce zaplatí, či umožní odklad splátek, ale nekřiví trh vléváním peněz do výrobního podniku, který si má sám dokázat vydělat. Dotace mají být určeny pro neziskovou sféru, pro kulturu, životní prostředí apod.,“ dodává.
Materiály jen z Evropy
Vzhledem k zahraničním zákazníkům musí firma vyrábět výhradně z materiálů s garantovanou vysokou kvalitou.
„Používáme celkem asi 20–25 typů různých plastů,“ objasňuje Tomáš Přeučil, vedoucí výroby. „Z toho 80–90 % je polypropylen, 10 % polyamid a zbytek pak kombinace všech možných plastů, protože pro automotive vyrábíme kontaktní systémy, kde menší díly mají 0,5 g. Jedná se o speciální materiály, takže portfolio plastu pro kontaktní systémy je obrovské, ale při malých objemech. K tomu zpracováváme i obrovské množství mosazi – 900 až 1 000 tun ročně. Všechny materiály, které dovážíme, pocházejí z Evropské unie. Mosaz je z 98 % z Itálie, něco málo z České republiky, protože české firmy, které tyto kovy zpracovávaly, v mnoha případech zanikly. Polypropylen, který zpracováváme, pochází z Itálie nebo z Finska, polyamidy jsou zpravidla německé. I kvalita zpracovávaných materiálů nám umožňuje udržet se v automotive, protože pokud by se firma z naší branže vydala cestou levných materiálů, do mnoha projektů se nedostane.“
Je třeba dodat, že v současné době je firma FMP ve výrobě uzavíracích prvků z PPR pro vodovodní rozvody pravděpodobně největším výrobcem v Evropě.
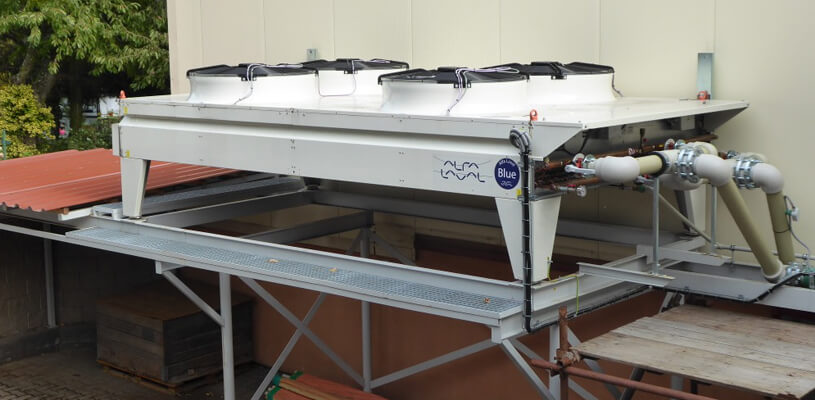
Efektivně topit i chladit
Významnou složku v provozních nákladech firmy tvoří úhrady za energie. Navíc konkrétně v provozovně v Ládví byly též problémy s dostatečnou kapacitou elektrické energie od dodavatele.
„Z těchto důvodů jsme přistoupili k projektu Úspory energie vyhlášeným ČMZRB,“ říká Vladimír Faber. „Současně s tímto projektem jsme realizovali projekt Expanze, který nám umožnil zavést další robotizaci a dále modernizaci nástrojařské dílny.“
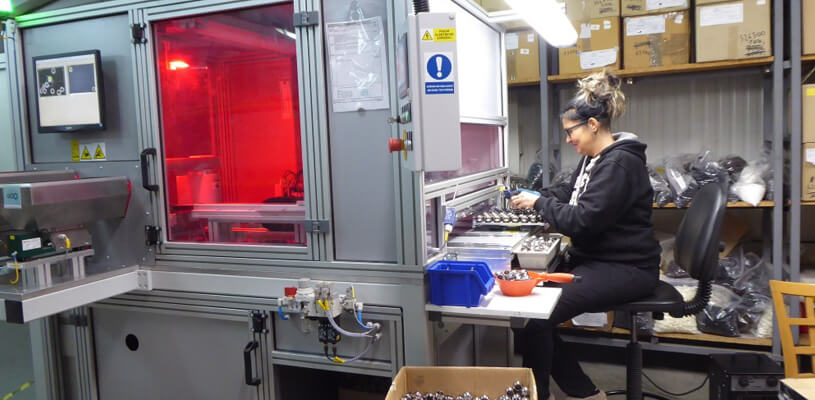
V rámci projektu Úspory energie vedení firmy pořídilo do provozovny Ládví moderní kotle od rakouské firmy Fröling. Díky svému velmi kvalitnímu řízení tyto kotle snižují potřebu obsluhy i spotřebu biomasy. V rámci téhož projektu zde pořídili chlazení od firmy Veskom, které kromě dodržení technologických postupů ještě spoří elektrickou energii.
„Někdo se koncentruje především na to, aby měl špičkové obráběcí časy, ale přitom má třeba neefektivní zateplení budovy,“ vysvětluje Tomáš Přeučil. „My jsme však šli oběma směry současně. Zefektivnili jsme vytápění prostor i chlazení forem a strojů, což znamená úspory vedlejších nákladů. Prakticky současně jsme zefektivnili výrobní procesy, tím, že jsme pořídili pro určitá místa naší výroby roboty nebo například stroj Arburg, který umožňuje vstřikování dvou materiálů současně. Jedná se nám také o ušetření lidské síly. Nejen proto, abychom mohli kvalifikované odborníky využít tam, kde je stroj nahradit nemůže. Důvodem je například i fakt, že jestliže máte možnost robotického zakládání výrobků, výrazně lépe udržíte cyklus i takt výroby, a tedy výslednou kvalitu,“ doplňuje jej Vladimír Faber a dodává: „A s tím opět úzce souvisí hospodaření s energií. Máme nyní striktně přesné režimy chlazení, takže výrobky nejsou ani přehřáté, ani podchlazené. Prostě přesně, jak mají být. Regulační proces, díky němuž toho dosahujeme, není jednoduchý. Nicméně díky souhře všech těchto opatření od nás zákazník dostává vysoce kvalitní díly.“
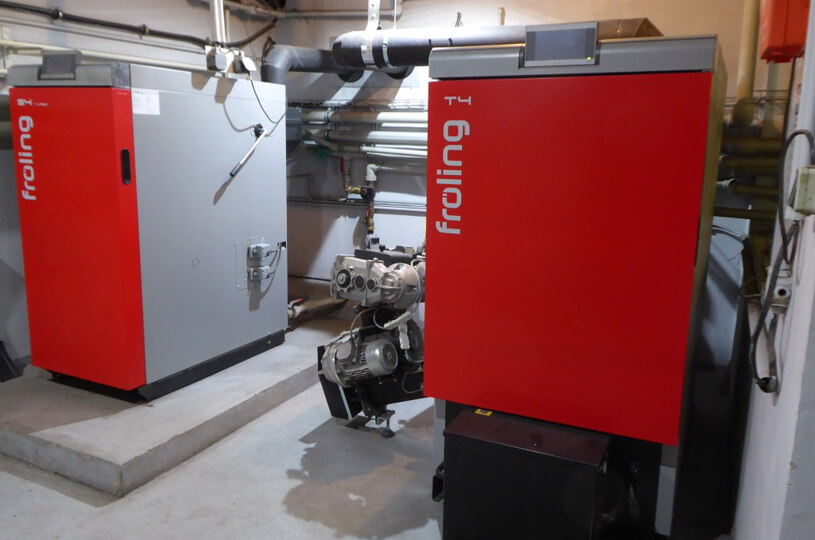
Úspory pro budoucnost
Vhledem k úspěšnosti předchozího projektu v provozovně v Ládví nyní vedení firmy plánuje pokračování v provozovnách Písek a Humpolec. Do provozovny Písek má v úmyslu pořídit moderní kotel na spalování kusového dřeva, včetně akumulace a řízení, a dále speciální dokončovací robot. Ten bude provádět dokončování výrobků v kratších časech. Dále je v plánu pořízení dvou kolaboratorních robotů, kteří poběží v nepřetržitém cyklu, bez prostojů způsobených lidskou obsluhou.
A FMP hodlá též i v provozovně Humpolec zefektivnit chlazení výměnou stávajícího jednookruhového systému za dvouokruhový a instalovat tzv. „freecooling“ – efektivní systém využívající chladu venkovního prostředí. Každé z plánovaných opatření mimo jiné významně ušetří energii.
Tři kroky k úspoře energie
V rámci energetické analýzy provozu, která měla identifikovat energeticky kritická místa, vhodné k zavedení účinných nápravných opatření, byly nalezeny tři vhodné možné realizace:
- Optimalizace spotřeby energií formou modernizace centrálního systému chlazení výrobních strojů, včetně systému Freecooling.
- Výměna části výrobního zařízení na lisování plastů. Dva zastaralé lisy typu CS byly nahrazeny dvoukomponentním lisem Arburg ALLRounder 470 S.
- Rekonstrukce zdrojů tepla a úpravy napojené otopné soustavy. Kotelna obsahovala celkem čtyři zastaralé kotle na biomasu, které byly na konci životnosti a měly nízkou účinnost. Byly nahrazeny dvěma vysoce účinnými, nízkoemisními kotli značky Fröling.
Přínosy – fakta a čísla
Především úspora spotřeby energie, ta by měla činit až 28,13 % ročně. S tím souvisí i relativně velké snížení finančních nákladů, takže doba návratnosti investice je poměrně krátká – 5,4 let.
Došlo také k příkonovému odlehčení provozu Ládví. Z hlediska životního prostředí a udržitelného rozvoje dojde ke snížení emisí CO2, a to ročně o cca 249 t. Nové technologie jsou vysoce moderní a uživatelsky přívětivé, díky tomu poklesnou i náklady na pravidelnou údržbu, především strojů (vstřikolisu) a nové kotelny. Celkově se uspoří dvě pracovní místa.
Modernizovaný chladicí systém nahradil starší málo efektivní, a jsou striktně oddělené a řízené dva okruhy chlazení pro formy a pro samotné stroje.
Kotelna, kromě úspory paliva, přinese i čistší, méně prašné prostředí a společnost FMP dokáže i nadále využívat zelenou biomasu z pozemků v okolí.
Kotle jsou s efektivním spalováním a nízkoemisní.
Náklady na obsluhu a údržbu kotelny se snížily až o polovinu a výstupy z nových kotlů jsou nízkoodpadové.
Dvoukomponentní vstřikolis přinese kromě energetické úspory i důležitou konkurenční výhodu, protože díky jeho pořízení lze vyrábět specializované výrobky, které firma ještě nedávno nebyla schopna produkovat = nové obchodní příležitosti na trhu.
Článek vyšel v časopise MM Průmyslové spektrum.